Overview
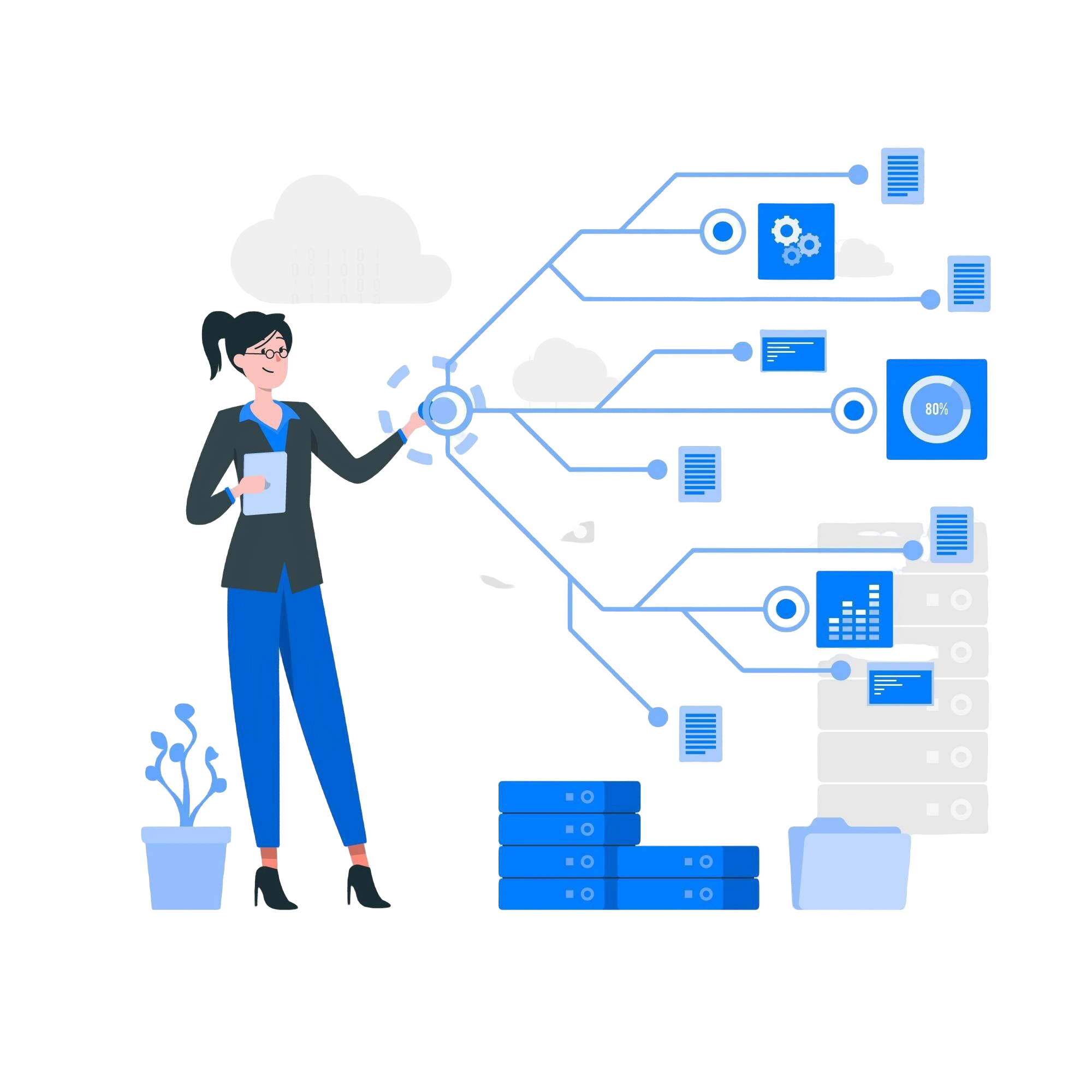
In the realm of oil and gas pipeline construction, welding plays a crucial role in ensuring the integrity and longevity of the pipelines. One of the leading companies working within this field approached Travancore Analytics with the objective to create a mobile application for welding machine which could interact with the machine and gather weld data in real time.
- Developed a solution that would replicate the welding process so that a connection to the machines could be initiated and the data transferred to the cloud.
- Able to collect and store various logs related to weld quality, coating, technical information, and so on.
- The solution positively impacted the client’s operations, enabling improved welding efficiency, data analysis, and quality control in their pipeline construction projects.
Case
The client, a company involved in welding pipes for oil and gas pipelines in remote field locations, needs a mobile application to connect to their welding machines and monitor the weld parameters. However, due to logistical challenges, they are unable to provide the physical welding machines for development and testing purposes. The challenge is to develop the mobile app without direct access to the welding machines and ensure accurate simulation of the welding process, data transfer via Bluetooth Low Energy (BLE), and cloud synchronization of the collected data.
Challenges
A significant challenge in developing the mobile app is the lack of direct access to welding machines, stemming from logistical constraints. This limitation complicates the ability to simulate real-world conditions during development. Another challenge involves the traditional method of monitoring welding parameters, which is often inefficient and lacks real-time insights. Since operations are conducted in remote locations with limited or no connectivity, the app must reliably capture and store data locally. This ensures that technicians can document and communicate essential details, even when addressing issues remotely, allowing for seamless data transfer once connectivity is restored.Solution
Most of these operations occur remotely and it was difficult to monitor and get the welding parameters. The client wanted a mobile application that ensure to get the details even if the technician fixes remotely. We have suggested a phase wise implementation approach and the initial phase of the application is developed to be capable of connecting to welding machines used for oil and gas pipelines. The pipe with machines on both sides know as “bugs” capture critical data like weld quality, technical logs and production logs.Since such operations tend to take place in locations with low or no connectivity, the team made sure that the functionality of the app could be performed offline and information was saved locally closer to the machine. The remarkable thing with this program is that once internet connection is available, the data is uploaded to the cloud. To make uninterrupted connection with the welding machine, the app employs BLE to obtain real-time data.
In addition, a C++ simulation module was created to mimic BLE communication and data transfer in order to enrich the solution. This enabled the team to check whether the collected data and communication protocol would work properly with the planned welding machines, without necessarily having to physically connect it or integrate it with the machines required to make it all work, seamlessly.
The team used mixed hybrid mobile development by employing the use of react native in the development of applications in both IOS and Google. To create a stable connection between the distributed mobile application and the welding machine, they included Bluetooth Low Energy (BLE) stack.
When choosing the cloud solution for updating as well as for storing data, the support of which is described above, we used AWS. Echoed in the UI/UX design, Adobe XD and Figma made it easy for the end users to use the Macro application.
Solution Highlights
- The developed mobile app enables technicians to connect to the welding machine, monitor welding parameters, and view real-time data during the welding process.
- It allows for the collection and storage of various logs related to weld quality, coating, technical information, and production details.
- The app ensures seamless data synchronization with the cloud, associating the data with specific projects, weld points, and unique identifications.
- The simulation module facilitated the app’s development, enabling efficient testing and validation of the app’s functionality without a physical welding machine.
Impact
The first phase of the application was successfully implemented to allow technicians to document welding parameters immediately after welding. Through the usage of this mobile app, the scope of the client’s portfolio was greatly enlarged, diminishing the field service application and giving flexibility to technicians so that they could record and analyse service activities and weld machine information.
Furthermore, the team also built a Power App PoC that could be of interest to the client’s IT part to explore more about internal tools. The successful outcomes of the first set of projects provided a basis for reference of subsequent projects, which showed that simulation, cloud integration, and consistent UI/UX were useful guiding principles in the development of high quality and scalable solutions