Overview
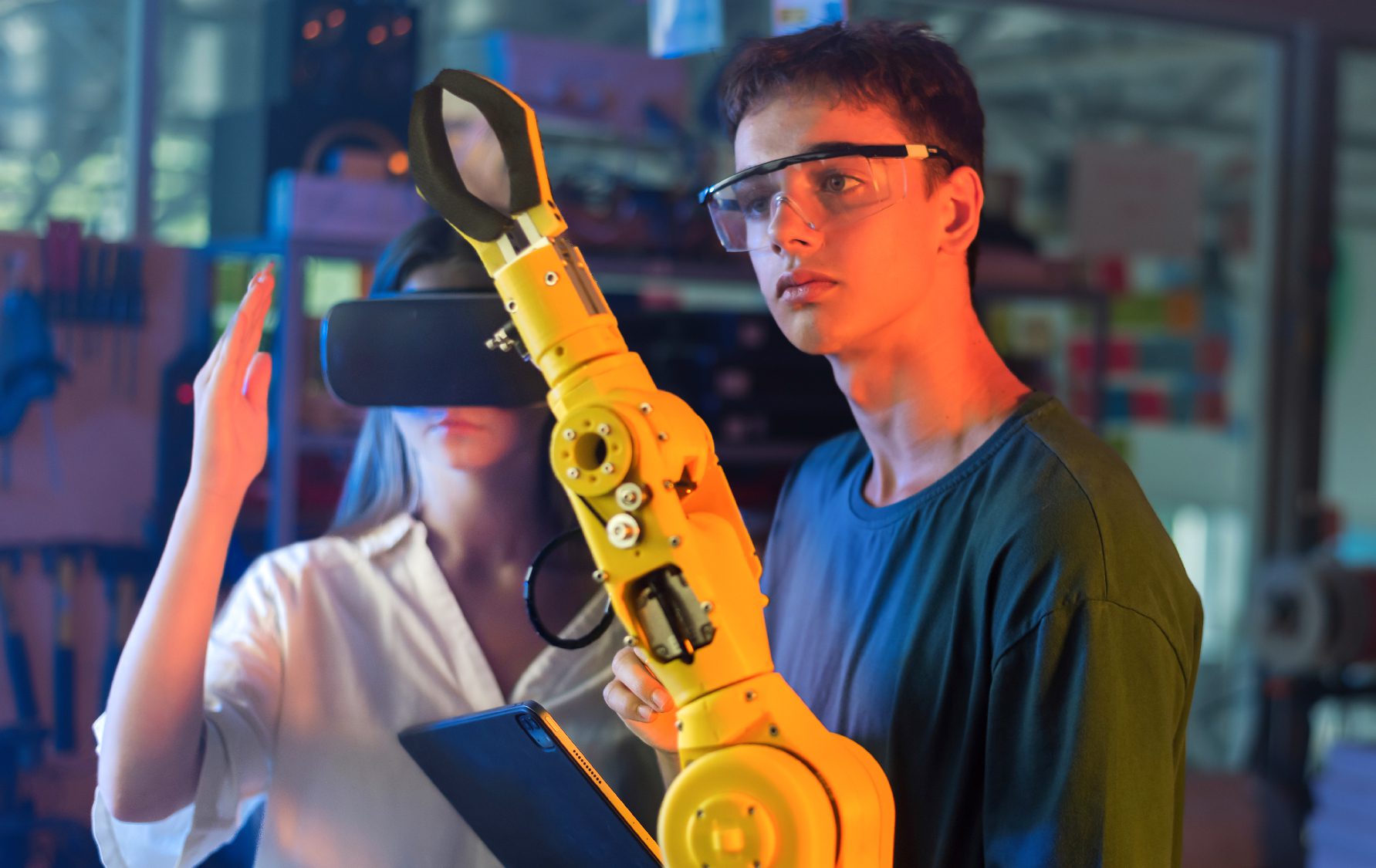
Enhance space operations and open new commercial ventures for future space innovations with 7 DoF robotic arms! Designed to endure environmental constraints, precision requirements, and the demand for reliability in extreme conditions.
- Gazebo and Rviz were used for simulations and early prototypes were thoroughly tested.
- Radiation-hardened brushless DC motor drives the robotic arm’s 7-axis configuration.
- The arm with the advanced kinematics module is built of carbon fiber composites or titanium alloys to boost reliability and flexibility in harsh environments.
- Redefines human exploration, bridging science and engineering for infinite possibilities.
Case
Industries increasingly rely on robotic systems for operations that are either too risky or impossible for humans to perform directly. Recognizing the growing demand for such technology, our team embarked on a pioneering project, collaborating with a government research agency to develop a space-standard robotic arm design from scratch. The project’s objective was a 7-DoF robotic arm design and development that could perform complex manipulations and repairs, assist in the assembly of different structures, and contribute to servicing missions.
Challenges
Developing a space-standard 7 DoF robotic arm design presented several significant challenges:- Environmental Constraints: The vacuum of space, extreme temperatures, and radiation presented unique challenges for the design and material selection.
- Precision and Realibility: The need for high precision in movement and operations, coupled with the demand for the utmost reliability in an environment where repairs are needed.
- White and Size Limitations: The costs associated with the missions necessitated a design that was both lightweight and compact.
- Power Efficiency: The robotic arm needed to operate efficiently with limited power resources available.
Solution
The development process was divided into several key phases:Conceptualization and Design: Initial design discussions focused on implementing the use case and achieving a balance between strength, flexibility, and weight. It was decided to develop a manipulator robot with 7 DoF. Advanced simulation tools like Gazebo and Rviz were used to model the robotic arm's behavior in various conditions.
Material Selection: Materials were chosen based on their durability, radiation resistance, and thermal properties. High-strength, lightweight alloys, and composite materials were predominantly selected.
Prototyping: Early prototypes were developed to test and refine the mechanical design and functionality. This phase included rigorous testing under different simulated conditions.
Integration of Electronics and Software: The development of custom control software and integration with high-precision sensors and actuators. Special emphasis was placed on creating fault-tolerant systems.
Testing and Validation: The robotic arm underwent extensive testing, including different simulated conditions and robotic operations, to ensure precision and reliability.
Design Specifications
- Number of Axes: The robotic arm was designed with a 7-axis configuration, providing the flexibility needed to mimic the range of motion of a human arm. This design choice was critical for ensuring the arm could navigate the complex environments of space operations.
- Controllers and Motors: Each axis needs to be powered by a high-torque, radiation-hardened brushless DC motor, chosen for its reliability and efficiency. The motors were controlled by custom-designed, fault-tolerant electronic controllers capable of precise movement adjustments and rapid response to commands. The motor controllers communicate with the main system using the CAN or RS485 interface. The system utilizes a Maxon EPOS4 disk 60/8 CAN-based controller and RS485 links are daisy-chained.
- Kinematics Module: The arm featured an advanced kinematics module, allowing for real-time calculations of the arm’s position, orientation, and velocity. This module was crucial for the accurate placement and manipulation of objects in space.
- Material Selection: The arm featured an advanced kinematics module, allowing for real-time calculations of the arm’s position, orientation, and velocity. This module was crucial for the accurate placement and manipulation of objects in space.
Software Integration
- ROS (Robot Operating System): The control architecture of the robotic arm was built on ROS, providing a flexible framework for software development. ROS facilitated easy integration of sensors and actuators, real-time control, and simulation capabilities. It also enabled modular software development, allowing for easy updates and scalability.
- Gazebo Simulation: The Gazebo simulation environment was used extensively throughout the development process. It allowed for the virtual testing of the robotic arm’s design and control algorithms in detailed simulations of space environments. Gazebo’s physics engine and ROS integration were pivotal in optimizing the arm’s performance before physical testing
System Overview
Adaption Process
- Material Selection: Replace existing aluminum and steel components with space-grade materials like titanium alloys or carbon fiber composites, considering strength, weight, and radiation resistance.
- Mechanism Redesign: Modify joint designs to accommodate thermal expansion and contraction due to extreme temperature variations. Optimize linkage mechanisms for stiffness and reduced weight.
- Actuator Selection: Replace existing electric motors with radiation-tolerant and high-efficiency brushless DC motors or alternative actuators like shape memory alloys.
- Sensor Integration: Integrate radiation-hardened sensors for position, force, and proximity feedback for precise control and collision avoidance.
- Control System Upgrade: Develop advanced control algorithms for autonomous operation, including inverse kinematics, trajectory planning, obstacle detection, and adaptive control for varying environments.
- Radiation Shielding: Implement shielding around critical electronics to protect them from radiation damage.
- Thermal Management: Design a passive or active thermal management system to maintain optimal operating temperature across all components.
- Dust Protection: Implement sealing mechanisms and filters to prevent dust intrusion into joints and actuators, ensuring smooth operation in dusty environments.
- Qualification and Certification: Rigorously test the adapted arm in simulated space environments and obtain necessary certifications for spaceflight safety and reliability.
Additional Considerations
- Maintainability: Design for in-orbit repair or self-repair capabilities using modular components and standardized tools.
- Redundancy: Implement redundancy in critical systems (e.g., dual motors, multiple sensors) to ensure arm functionality even if individual components fail.
- Human-Robot Interaction: Consider interfaces for human control or collaboration with the arm for complex tasks.
Results
The project will culminate in the development of a robotic arm that will meet all the specified requirements for space operations:
- Precision and Flexibility: It will achieve high precision in operations with the ability to manipulate a wide range of tools and components.
- Durability: It is expected to demonstrate robustness in extreme conditions, ensuring long-term reliability.
- Efficiency: It is to be operated within the power constraints of space missions, maximizing efficiency
Innovation: Introduced several innovative solutions, including a unique joint design for increased flexibility and a modular construction allowing for easy upgrades and repairs.
Impact
The development of the space standard robotic arm represents a significant advancement in space robotics, with broad implications for the future of space exploration and operations.
- Enhanced Space Operations : The robotic arm is expected to play a crucial role in satellite servicing, space construction, and repair missions, significantly expanding the capabilities of space missions.
- Commercial Opportunities : The technology developed opens up new avenues for commercial ventures in space, including satellite maintenance and debris removal services.
- Research and Development : The project has contributed valuable insights into the design and operation of robotic systems in space, paving the way for future innovations in the field.
Conclusion
The successful development of the space standard robotic arm from scratch marks a milestone, combining cutting-edge engineering with innovative design to meet the unique challenges of space operations. As the arm moves from development to deployment, it stands as a testament to the potential of robotic systems to extend human reach and capabilities in space.