February 24th, 2025
Category: Artificial Intelligence,Manufacturing
No Comments
Posted by: Team TA
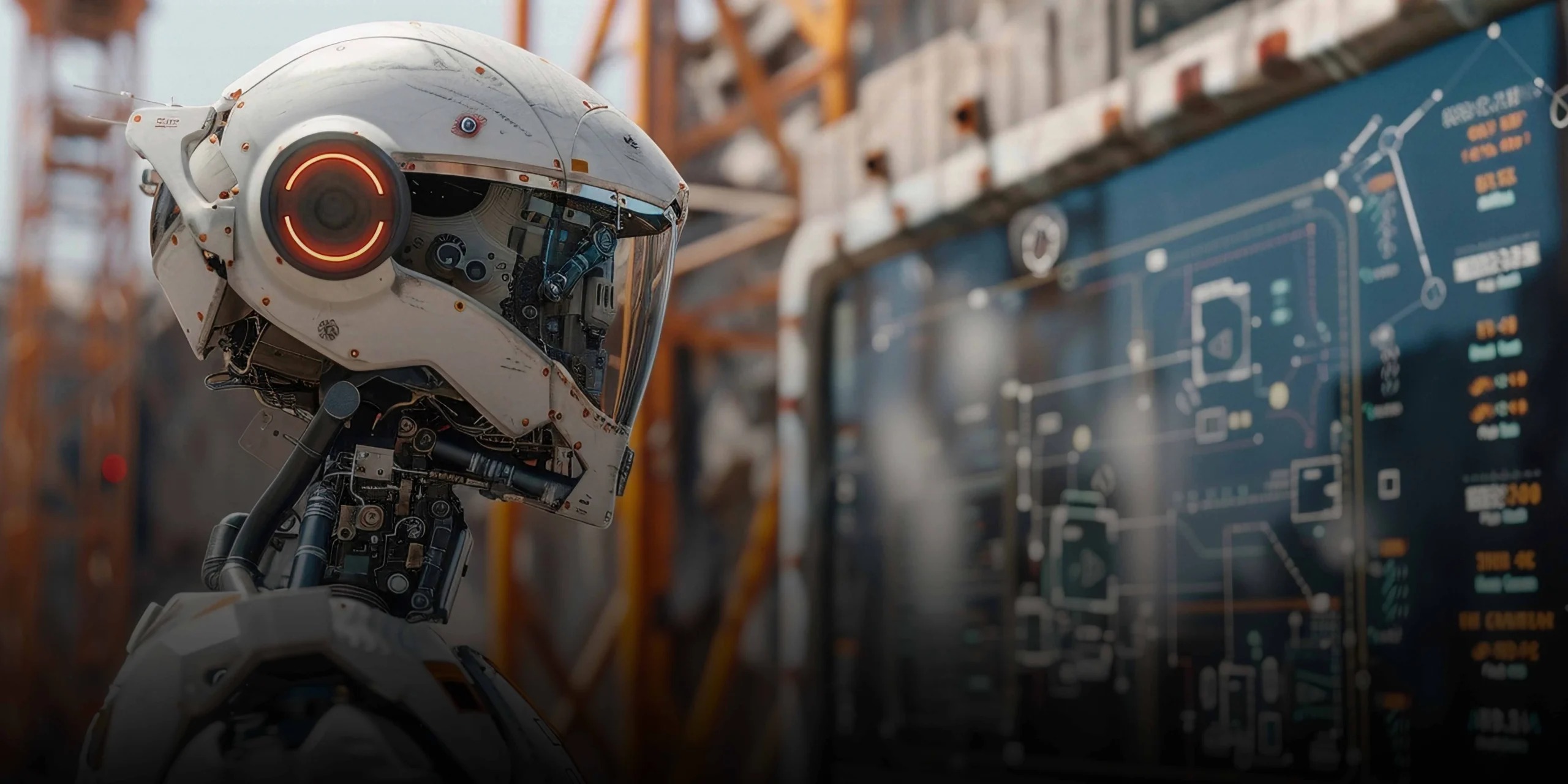
The manufacturing industry, a pioneer in embracing computer technology since the 1970s, is now at the forefront of the AI revolution. As we enter the age of Industry 4.0, artificial intelligence is rapidly transforming how goods are produced. AI offers unparalleled capabilities for analyzing this information and optimizing production processes. Based on Deloitte’s survey on AI in manufacturing industry, the manufacturing sector generates an estimated 1,812 petabytes of data annually. Recognizing the transformative potential, 93% of manufacturing companies surveyed by Deloitte believe AI will be crucial for driving future growth and innovation within the industry.
What is AI in the Manufacturing Industry?
Artificial Intelligence (AI) in the manufacturing industry refers to the integration of advanced machine learning algorithms, computer vision, robotics, and data analytics to automate and optimize various aspects of production. Unlike traditional automation, AI systems can learn from data, adapt to changing conditions, and make real-time decisions—enabling smarter, faster, and more flexible manufacturing operations.
From predictive maintenance that prevents costly equipment failures to AI-driven quality control systems that catch defects with higher accuracy than human inspectors, AI is revolutionizing how manufacturers design, produce, and deliver goods. As the backbone of Industry 4.0, AI is not just a tool—it’s a transformative force that enhances operational efficiency, reduces costs, boosts product quality, and drives sustainable growth.
How AI being Used in the U.S Manufacturing Industry?
AI is being applied through technologies such as collaborative robots (cobots), computer vision, digital twins, and generative AI. These innovations are driving improvements in areas like demand forecasting, equipment reliability, energy efficiency, and worker safety. For instance, AI can predict when a machine is likely to fail, optimize factory workflows, or detect product defects more accurately than human inspectors.
Discover how AI is transforming the manufacturing industry—explore the applications, key benefits, major challenges, and essential steps to secure sensitive data and boost productivity.
1. Cobots and Autonomous Mobile Robots
Manufacturers are increasingly adopting advanced robotics, such as collaborative robots (cobots) and autonomous mobile robots (AMRs), to enhance workforce efficiency, reduce errors, and improve quality. Rockwell Automation’s 9th Annual State of Smart Manufacturing report reveals that 85% of companies have either invested or plan to invest in AI/ML in these areas this year.
Amazon exemplifies this trend, utilizing over 750,000 robots alongside employees. Its Sequoia robotic tool accelerates inventory storage by 75%, reducing fulfillment processing time by 25% and enhancing shipping predictability for faster deliveries. Drones are also gaining prominence, according to ABI Research.
2. Supply Chain Management
AI improves supply chain management in several ways. Firstly, it utilizes massive amounts of data to accurately predict customer demand, allowing businesses to optimize inventory levels and efficiently manage the flow of goods. AI combined with digital twin technology allows companies to simulate different scenarios, such as unexpected disruptions or shortages, and find the best ways to address them.
Machine learning, a subset of AI, plays a crucial role in improving demand forecasting and automating the process of ordering materials. AI also streamlines order management, ensuring timely deliveries to customers. For example, food manufacturers can use AI to anticipate changes in demand during different seasons, reducing food waste and optimizing the use of resources.
For instance, Walmart’s AI-powered Route Optimization SaaS helps businesses streamline routes, pack trailers efficiently, and reduce miles. This technology saved Walmart 94 million pounds of CO₂ and avoided 30 million unnecessary miles.
3. Factory in a Box: AI-Powered Modular Manufacturing
The “factory in a box” concept involves modular, self-contained manufacturing units equipped with AI-driven automation, IoT sensors, and real-time data analytics. These portable units enable localized production, reducing logistics costs and allowing companies to respond swiftly to changing demands.
Industries such as electronics, automotive, and pharmaceuticals are already exploring this innovative approach, which shows potential to become a mainstream solution with advancements in automation, modular design, and data integration.
4. Predictive Maintenance
AI can predict when factory equipment might fail, preventing costly breakdowns. Using digital twins to monitor machinery behavior, AI systems can detect signs of trouble early on, alerting workers before problems occur.
For example, automobile manufacturers use predictive maintenance on assembly-line robots, reducing unplanned downtime and saving costs. This allows them to schedule maintenance during non-peak hours, minimizing disruption to production. By analyzing data like vibrations, heat signatures, and oil conditions, AI accurately assesses machine health, ultimately improving efficiency and saving money.
5. Inventory and Order Management
AI helps manufacturers keep just the right amount of stock on hand. By analyzing data, AI can predict future demand and automatically order more supplies when needed. By tracking inventory in real-time, businesses can reduce carrying costs, avoid overstocking, and improve cash flow.
A practical example is IBM Watson Orchestrate, which streamlines procurement through automation and conversational AI. It enhances vendor, contract, and order management. This allows the teams to integrate systems seamlessly, improve efficiency, and focus on strategic sourcing.
6. Quality Control
AI is revolutionizing testing and quality control by using image recognition to detect equipment damage and product defects. AI models analyze product images to identify flaws, deciding if items need rework or recycling. By examining production data and customer feedback, AI improves processes, reduces waste, and ensures better product quality with greater accuracy than human inspections.
A notable example is Huawei’s AI-powered quality Inspection Solution, which leverages advanced technologies like AI, cloud computing, and big data. Deployed across over 200 production lines, it includes more than 800 industrial-grade image-processing tools. Applied in industries like automotive and electronics, it enhances precision, efficiency, and reliability.
7. Generative AI for Manufacturing Documentation and Training
Generative AI simplifies manufacturing by making technical information easier to understand. It analyzes and summarizes complex documents, creating easy-to-follow guides for workers. For example, it can provide step-by-step instructions on how to fix an overheating machine. This reduces errors and saves time, ensuring the production line runs smoothly.
5 Key Benefits of Using AI in Manufacturing Industry
1. Increased Operational Efficiency
AI boosts manufacturing efficiency by automating repetitive tasks, allowing employees to focus on other important tasks. It improves productivity by optimizing workflows, reducing errors, and streamlining processes. With predictive analytics, manufacturers can prevent downtime and address issues proactively. This enables faster production without compromising quality while making better use of resources and time.
2. Improved Product and Customer Experience
AI enhances customer experience in manufacturing by analyzing data to understand customer preferences and personalize products. It ensures smooth operations through predictive maintenance and quality control, reducing failures and interruptions. By learning from continuous feedback, AI helps manufacturers refine processes and improve overall customer satisfaction.
3. Better Product Quality
By enhancing quality control, reducing defects, and providing real-time feedback, AI improves manufacturing quality. It also enables rapid prototyping, helping identify and fix design flaws early in product development.
4. Cost Reduction
AI enhances cost-effectiveness in manufacturing by optimizing supply chains, improving demand planning, and reducing waste. Technologies like digital twins and predictive maintenance extend equipment life, saving costs. AI also conserves resources like energy and water while streamlining operations for more efficient production.
5. Environmental Sustainability
In sustainable manufacturing, AI optimizes resource allocation, reduces energy use, and minimizes waste. Improving logistics and warehouse management helps lessen the ecological footprint. Self-monitoring components further reduce maintenance needs, promoting environmentally friendly practices.
What are the Challenges of Implementing AI in Manufacturing?
1. Data Quality and Availability
One challenge of using AI in manufacturing is the need for clean, accurate, and structured data. Poor-quality or fragmented data can lead to unreliable insights and suboptimal outcomes. Manufacturers must harmonize and consolidate data to ensure AI models perform effectively and provide actionable insights for various users.
2. Safety, security, and Responsible Use of AI
Using AI in manufacturing requires strong regulations to protect sensitive data and ensure ethical practices. Manufacturers should choose AI providers committed to transparency, responsible development, and data security. This includes avoiding data sharing with third parties, employing advanced security measures, and maintaining ethical standards to address risks like cybersecurity threats and IP theft.
3. Shortages of Skilled Labor
A shortage of AI and data science experts makes adopting AI in manufacturing challenging. Companies must invest in workforce development, using AI-powered tools to upskill employees. AI can also help by streamlining hiring processes and enabling employees to upskill using AI-powered learning tools.
4. Operational Risks
AI models, like generative AI, are still evolving and may lack the precision required for high-accuracy manufacturing tasks. This can be a challenge in ensuring reliability and consistency in production processes.
Cybersecurity Risks in Industrial AI for Manufacturing
Manufacturers are exposing themselves to new cybersecurity risks as they use AI increasingly to improve efficiency through automation, quality control, and predictive maintenance. Since AI systems are frequently cloud-based, they need external network connections, which could provide hackers with entry points. These connections pose major risks to the entire supply chain because, without appropriate security measures, they can give hackers access to private operational systems, halt production, and steal intellectual property.
Furthermore, cybercriminals are now using AI to expand the scope and accuracy of their attacks. AI-generated phishing or automated vulnerability scans can get past conventional defenses, and legacy systems that are difficult to patch become easy targets. These dangers can have serious repercussions if ignored, including ransomware attacks, data breaches, or even physical damage to infrastructure.
Impact of Cyber Breaches
Manufacturing processes can be seriously disrupted by cyberattacks on industrial AI systems. Production lines may be stopped for days or even weeks by a single attack, resulting in large financial losses. The average cost of a data breach in the industrial sector was USD 5.56 million in 2024, according to the IBM Cost of a Data Breach report. This reflects an 18% increase from the previous year.
Production halts, system recovery costs, and possible ransom payments are examples of direct effects. A factory that produces $100,000 per day, for instance, might lose $1.4 million if it were to close for two weeks. Other hidden costs are not included in these losses.
In addition to financial losses, breaches harm a brand’s reputation and undermine consumer confidence, which prolongs and complicates recovery. This emphasizes how urgently robust cybersecurity defenses are needed.
10 Steps to Mitigate Risks and Protect Sensitive Data in Industrial AI
1. Limit Remote Access Tools
Multiple remote access solutions are frequently used in manufacturing facilities, which raises the risk of security flaws. It is possible to reduce complexity and potential vulnerabilities by limiting the number of remote access vendors and tools. A simplified configuration is easier to secure and monitor.
2. Avoid Always-Active Connections
Remote connections that are always on are extremely susceptible to unauthorized access. Manufacturers should use remote access only upon request. To limit the attack window for cybercriminals, these connections need to be closely monitored and used only when permitted.
3. Ensure Rapid Disconnection Capabilities
Being able to swiftly cut off external connections is essential in the case of a cyberattack. Rapid isolation is an essential part of any incident response strategy because it helps stop threats from spreading throughout the network and allows for quicker containment and recovery.
4. Secure External and Cloud Access Points
Protecting external access points is crucial because a lot of AI models are hosted in the cloud. This includes setting up firewalls, access controls, and robust encryption. These access points are protected from evolving threats by undergoing regular audits.
5. Patch and Update Legacy Systems Regularly
The lack of modern security features commonly found in legacy systems makes them particularly vulnerable to cyberattacks. Patching and updating these systems with security updates improves the overall security posture and helps fix known vulnerabilities.
6. Implement AI-Specific Cybersecurity Frameworks
Security measures for AI systems must be customized to fit their operations and data flows. AI-specific cybersecurity frameworks, such as data integrity controls, threat detection systems, and secure coding techniques, should be created and implemented by manufacturers.
7. Anonymize Sensitive Manufacturing Data
To reduce the impact in the event of a breach, operational data should be anonymized before being sent to AI systems. Anonymization aids in preventing the exposure or misuse of sensitive information, including personal data and intellectual property.
8. Use Multi-Factor Authentication (MFA)
By asking users to confirm their identity using multiple methods, multi-factor authentication provides an additional layer of security. It greatly lowers the possibility of illegal access to vital network infrastructure and AI systems.
9. Monitor and Audit Continuously
Real-time detection of anomalous activity in network environments and AI systems is made possible by continuous monitoring. Frequent audits facilitate quicker risk mitigation by identifying weak points and ensuring adherence to cybersecurity policies.
10. Educate Staff and Vendors
One of the largest threats to cybersecurity is still human error. Frequent training for staff members and outside vendors guarantees that everyone is aware of security best practices and procedures, which lowers the possibility of unintentional breaches or risky behavior.
What is the future of AI in Manufacturing Industries?
The future of AI in manufacturing is poised to be transformative, driving a shift from automated to truly intelligent production systems. As technologies like machine learning, computer vision, digital twins, and generative AI continue to mature, manufacturers will rely more heavily on AI not just to streamline operations—but to innovate, adapt, and compete in a dynamic global market.
In the coming years, AI will play a central role in enabling:
Hyper-Automation: AI-powered robots and autonomous systems will handle increasingly complex tasks, from precision assembly to real-time quality control, reducing human error and increasing output.
Self-Optimizing Factories: Smart factories will continuously analyze performance data and automatically adjust processes to improve efficiency, reduce energy consumption, and minimize waste.
Predictive and Prescriptive Maintenance: AI will not only predict when machines might fail but also recommend the best course of action to prevent downtime and extend equipment life.
Sustainable Manufacturing: AI will help optimize resource usage, reduce carbon emissions, and support green manufacturing practices by enabling data-driven sustainability strategies.
Human-AI Collaboration: Workers will be empowered by AI tools—such as generative AI for documentation and AR-based training—to make better decisions, learn faster, and focus on high-value tasks.
As AI becomes more accessible and integrated with IoT, edge computing, and cloud platforms, even small and mid-sized manufacturers will be able to deploy intelligent systems. However, with this progress comes the growing need for strong cybersecurity, ethical AI practices, and upskilling the workforce to thrive in the age of Industry 4.0.
Final Thoughts
In summary, artificial intelligence (AI) is transforming manufacturing by increasing efficiency, improving quality, and reducing costs. From predictive maintenance and quality control to real-time decision-making and human-robot collaboration, AI drives smarter, more sustainable production. By leveraging AI technologies, manufacturers can optimize processes, increase productivity, and stay competitive in an evolving industry. As a leading AI app development company, Travancore Analytics specializes in creating impactful AI-driven software solutions for various industries.