May 26th, 2025
Category: Digital Twin
No Comments
Posted by: Team TA
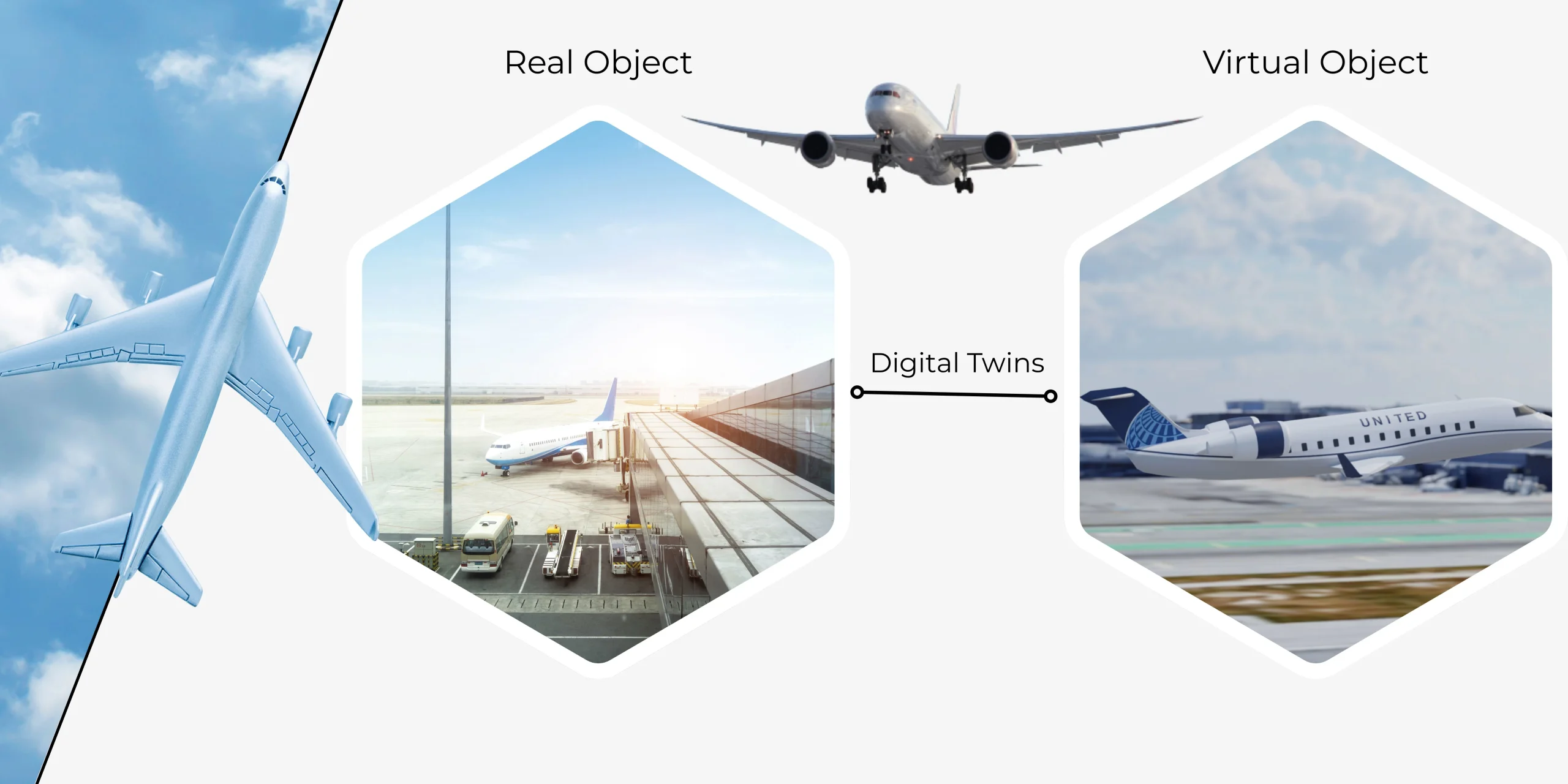
In a rapidly evolving manufacturing environment, where labor shortages and supply chain interruptions are frequent, digital twins offer real-time replicas of factories, equipment, and systems. These models enable manufacturers to simulate operations, predict maintenance needs, and test new strategies before implementation. The worldwide digital twin market is expected to expand at an impressive compound annual growth rate (CAGR) of 61.3%, from USD 10.1 billion in 2023 to USD 110.1 billion by 2028, according to MarketsandMarkets research.
With major companies like BMW and Renault incorporating digital twins in manufacturing processes, this technology is no longer a future concept but a present reality. This article examines how digital twins are transforming manufacturing, tackling challenges, and unlocking new opportunities.
What is a Digital Twin in Manufacturing?
A digital twin in manufacturing is a digitally produced model of an actual machine, system, or production process. To accurately represent the behavior and condition of the physical counterpart, it collects real-time data from sensors and Internet of Things (IoT) devices. This technology allows manufacturers to monitor operations, identify inefficiencies, and test improvements in a risk-free virtual environment before applying them to the actual production floor.
During every stage of the manufacturing process, from product design and prototyping to production and maintenance, digital twins are essential. Manufacturers can improve efficiency and productivity by forecasting equipment failures, optimizing processes, and making well-informed decisions through the simulation and analysis of various scenarios.
Benefits of Using a Digital Twin in Manufacturing
1. Superior Predictive Maintenance
In the manufacturing industry, unplanned downtime can lead to significant financial losses. Digital twins create virtual models of machines, enabling real-time monitoring and analysis. By simulating performance and identifying early signs of wear, manufacturers can predict failures and schedule maintenance proactively, minimizing production disruptions.
The integration of IoT devices enhances predictive maintenance by offering insights into machine health under various operating conditions. This approach reduces repair costs and ensures smoother manufacturing operations, ultimately improving efficiency.
2. Improve Operations
Digital twins enhance manufacturing operations by creating virtual models of production processes. These models enable monitoring of workflows, efficiency analysis, and identification of improvement areas. The digital twin identifies inefficiencies, suggesting strategies for reducing waste.
Additionally, they facilitate continuous tracking of machine performance, allowing manufacturers to fine-tune operations for improved efficiency and sustainability. Insights gained from digital twins also support equipment lifecycle management, aiding in maintenance planning and informed investment decisions.
3. New Hire Training
New hires can interact with a digital replica of the factory, equipment, and processes, allowing them to gain practical knowledge without disrupting operations. This accelerates learning and builds confidence before employees step into the physical workspace.
One key advantage is the ability to simulate real-world scenarios, including emergencies that are difficult or unsafe to replicate in a live setting. This prepares employees to handle challenges efficiently, improving problem-solving skills and overall workplace safety while ensuring a smoother transition into their roles.
4. Augmented Product Development
By generating replicas of production processes, digital twins improve manufacturing operations. These models make it possible to track workflows, analyze efficiency, and pinpoint areas for improvement. By highlighting inefficiencies, digital twins suggest strategies that optimize resource use and reduce waste.
They also make it easier to track machine performance continuously, which enables manufacturers to optimize operations for increased sustainability and efficiency. Digital twin insights also assist with equipment lifecycle management, supporting well-informed investment choices and maintenance scheduling.
5. Improved Collaboration
Digital twins foster seamless collaboration among teams across diverse locations by creating a shared virtual environment. This enables engineers, designers, and operators to interact with digital models, provide real-time feedback, and make informed decisions, ultimately streamlining workflows and accelerating project timelines. Stakeholders access up-to-date information remotely, enhancing communication, ensuring alignment, and facilitating knowledge sharing among global teams.
6. Streamline Costs
Digital twins enable manufacturers to reduce expenses by streamlining production and reducing waste. Virtual simulations make design testing, workflow optimization, and inefficiency identification easier, resulting in more intelligent resource management. Additionally, they make predictive maintenance and effective inventory control possible, eventually resulting in significant cost savings and raising overall profitability.
Digital Twin Use Cases in Manufacturing
1. Product Design
Digital twins are virtual models of products or manufacturing processes that help design new items. By using these digital versions, engineers can experiment with different designs and test how they will work without building a physical model first. This saves time and money.
Additionally, digital twins gather real-time data to improve product quality and tailor designs to meet customer needs. Overall, they speed up development and encourage innovative ideas in manufacturing.
2. Supply Chain Management
Digital twins play an important role in supply chain management by creating accurate digital representations of products and processes. This allows businesses to monitor every step of the supply chain in real-time, improving visibility and efficiency.
With digital twins, companies can quickly identify potential issues and adjust their operations, accordingly, ensuring smooth delivery and reducing delays. This technology helps optimize resources, leading to better decision-making and enhanced overall performance in the supply chain.
3. Process Design and Optimization
By simulating various performance conditions, digital twins help manufacturers design and optimize processes. This enables them to move from a reactive to a proactive approach by predicting and removing potential issues before they arise. Manufacturers can optimize processes, boost productivity, and lower operational risks by evaluating real-time data.
Digital twins have been effectively used by businesses such as Siemens to maximize output, minimize waste, and lower energy consumption. Manufacturers can reduce expenses and speed up innovation by locating bottlenecks and improving workflows.
4. Equipment Monitoring
Digital Twin technology is transforming manufacturing by allowing companies to monitor their equipment from anywhere in real-time. This means they can keep an eye on their machines without needing to be physically present.
By using this technology, manufacturers can predict when a machine might need maintenance, helping to avoid unexpected breakdowns and costly downtime. This leads to smoother operations and more efficient use of resources.
5. Tours and Guests
Digital twins are changing how manufacturers manage tours and guests. With a 3D digital model of the facility, visitors can explore the space virtually on their devices, even using VR headsets. This means they can experience the environment without disrupting operations. It allows manufacturers to showcase their processes safely while keeping their production areas distraction-free and efficient.
Identifying Common Challenges in Digital Twin Implementation
1. Data Integration and Quality
The effectiveness of a digital twin depends on the quality and consistency of the data it receives. However, integrating data from multiple sources within a manufacturing system can be challenging. Differences in data formats, siloed information, and inconsistent data quality can lead to inaccurate digital models, making it difficult to generate reliable insights for decision-making.
2. Costs and Investments
Adopting digital twin technology in manufacturing requires significant investment in sensors, IoT devices, software, and skilled professionals. While the long-term benefits can be substantial, the high initial costs often pose a barrier for many manufacturers. Ensuring a strong return on investment is crucial for successful implementation and widespread adoption.
3. Complexity of Models
It can be very difficult to create precise digital twin models that accurately depict actual manufacturing procedures. Manufacturers may encounter difficulties like scope creep, higher expenses, and longer timelines as they develop their digital twin capabilities. To keep the implementation on track, managing this complexity calls for proficiency in data modeling, simulation, and efficient project coordination.
4. Security and Privacy Concerns
Digital twins rely on enormous amounts of data, so security is crucial. It is essential to defend tangible assets, intellectual property, and sensitive data from online attacks. Manufacturers must put robust cybersecurity measures in place to guard against data breaches and guarantee the secure operation of their digital twin environments as interconnected systems expand.
Conclusion
Digital twins are transforming how manufacturers operate by providing a detailed virtual view of processes and systems. This innovative technology helps organizations make informed decisions and stay competitive in a rapidly changing market. Understanding how to effectively implement and integrate digital twins is crucial for manufacturers aiming to improve efficiency and overcome challenges.
To maximize the benefits of digital twin technology in manufacturing, companies need a solid plan covering data management, network capabilities, and security measures. The key is ensuring that the digital twin solution is flexible and scalable to adapt to evolving business needs. Partnering with the right experts can provide the necessary guidance and insights.
By choosing Travancore Analytics, manufacturers can leverage industry knowledge and technical expertise tailored to their specific requirements. Explore how partnering with TA can elevate your operations—let’s work together to create efficient and effective digital twin solutions for your organization.