April 30th, 2025
Category: Digital Twin
No Comments
Posted by: Team TA
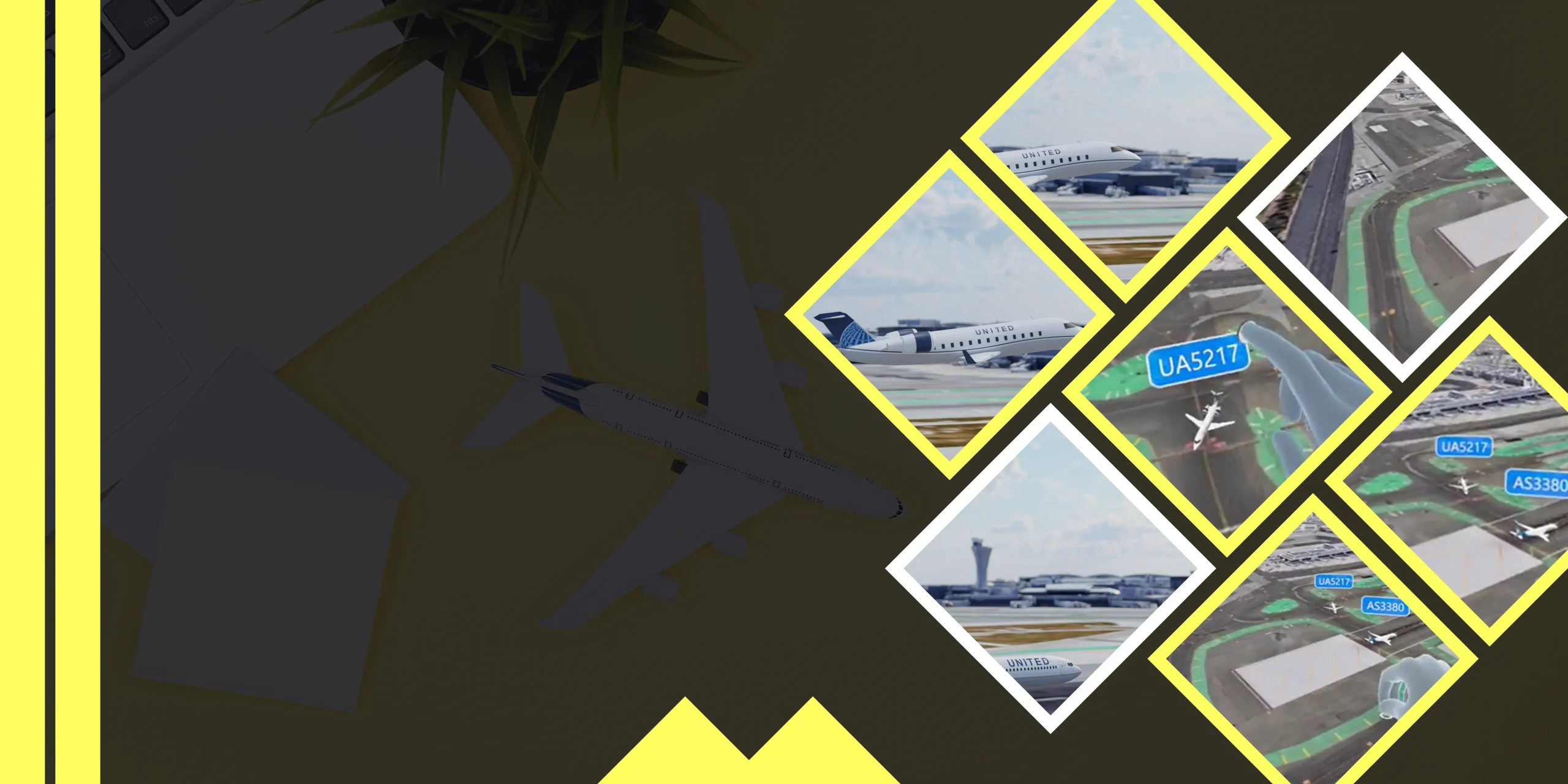
Digital twins are transforming industrial automation by bridging the gap between physical assets and digital intelligence. These advanced virtual models improve manufacturing efficiency, safety, and decision-making. The global digital twin market is expected to expand at a compound annual growth rate (CAGR) of 39.8% from €16.42 billion in 2024 to €240.11 billion by 2032, with manufacturing emerging as the fastest-growing sector, according to Fortune Business Insights. With the help of this game-changing technology, manufacturers can now access real-time insights for better resource management and operational optimization.
Digital twins, which are dynamic virtual representations of manufacturing systems, help with real-time optimization, predictive maintenance, and innovation. They enable teams to effectively test and enhance processes by serving as a digital sandbox. In this blog, we’ll explore how digital twin technology is transforming industrial automation and helping manufacturers overcome key challenges to unlock greater value.
Smarter Technology for a Smarter Future
Automation is becoming smarter, faster, and more efficient thanks to digital technology, which is changing the way manufacturers operate. Companies are now utilizing tools like advanced analytics and predictive maintenance to improve operations as part of the Industry 4.0 wave. But when it comes to managing the vast volumes of data required for complete automation across multiple machines or production lines, conventional systems frequently fail.
To solve this, many are turning to digital twins—virtual models that replicate physical assets and processes. These smart models bring together scattered data, simulate real-world behaviors, and help teams make better decisions. A 2023 Forrester report for Hexagon states that 67% of manufacturing tech leaders will give digital twins top priority for enhancing the sustainability of the product lifecycle, while 65% of them intend to use them to optimize operations.
Key Benefits of Digital Twins in Industrial Automation
1. Real-Time Monitoring and Control
The effectiveness of digital twins for manufacturing automation depends critically on real-time data integration. A digital twin gets regularly updated with real-time data from sensors and devices. This real-time flow guarantees that the twin accurately reflects its real-world counterpart, enabling accurate monitoring and quicker, more intelligent decision-making.
Digital twins help reduce downtime and prevent unplanned breakdowns by instantly detecting problems like machine wear. This proactive strategy increases productivity, facilitates predictive maintenance, and enhances team communication.
Real-time insights connect the digital and physical worlds, enabling manufacturers to work together, improve operations, and quickly respond to changes—all from one updated source.
2. Advanced Predictive Maintenance
By mimicking real-world situations to forecast how equipment will operate, digital twins provide strong support for predictive maintenance in manufacturing. In addition to avoiding expensive trial-and-error in the physical environment, this aids manufacturers in making quicker, more informed decisions. Additionally, it saves resources and shortens time to market.
Unexpected machine failures can reduce profits and cause production disruptions. Digital twins connected to repair histories, manuals, and real-time data from IoT sensors make it easier and faster for technicians and operators to identify and fix problems.
Digital twins can identify trends in machine behavior and anticipate failures before they happen by utilizing AI and machine learning. This proactive maintenance strategy increases equipment longevity, reduces expenses, and avoids unscheduled downtime.
3. Enhanced Process Modelling and Simulation
Digital twins employ advanced process models to mimic real-life manufacturing activities, allowing for the simulation of various scenarios and behaviors within the process. These models provide a clear way to assess and enhance processes by simulating ideal future states and assisting in the visualization of existing conditions.
Using digital twins helps monitor equipment. This technology allows manufacturers to improve machine operations. They can test different situations to find the best ways to use their machines. This leads to saving energy, less wear and tear, and better product quality.
4. Improved Safety and Training
By providing a secure, engaging virtual environment where workers can learn and practice operations without the risks of the real world, digital twins improve workforce training. This practical experience expedites the learning process and boosts confidence.
Additionally, a variety of real-life situations, such as emergencies that would be hazardous to physically recreate, can be simulated using these virtual models. This improves workers’ ability to make decisions and helps them get ready for unforeseen obstacles.
Standardized training for digital twins can be readily resized or modified for various locations and guarantees uniform learning across teams. Manufacturers are creating a workforce that is safer, more intelligent, and more capable by investing in this strategy.
5. Better Design Planning
Designers can rapidly test and improve concepts without creating physical prototypes by using digital twins. This speeds up development and lowers costs, making design more flexible and innovative.
Teams can collaborate in real time on the digital twin, no matter where they’re located. Everyone can view designs, provide feedback, and make more informed decisions more quickly, including engineers.
By spotting design flaws early, digital twins help avoid expensive mistakes and support sustainable choices by optimizing materials and energy use. This leads to smarter, greener products and a more efficient design process.
6. Enhanced Tours and Guest Experiences
Production tours become immersive, interactive experiences thanks to digital twins. The ability to interact with simulated processes, examine virtual models, and learn more about how operations function makes visits more interesting and instructive.
Digital twins give educators and students a practical learning tool that gives them an inside look at industrial automation. This prepares future workers and encourages interest in STEM fields.
Through the visual display of facility operations and innovations, they also assist manufacturers in establishing connections with stakeholders. Additionally, using digital twins in tours supports branding by emphasizing the company’s commitment to cutting-edge technology—attracting customers, partners, and future talent alike.
Wrapping Up
Manufacturing is being reshaped by digital twin technology, which provides virtual models that replicate real-life machinery and processes. By allowing testing and validation before actual production, these models improve efficiency, cut down on waste, and save time. Manufacturers can increase the agility and cost-effectiveness of their processes by simulating operations and optimizing results without physically handling assets.
A major advantage is that digital twins integrate seamlessly with existing Manufacturing Operations Management (MOM) systems. Manufacturers can increase the value of their legacy infrastructure by adding digital twin technology on top of it rather than replacing it. This facilitates rapid implementation, frequently in a matter of months, and speeds up return on investment.
Digital twins give manufacturers the ability to innovate more quickly, adapt more quickly, and get ready for the challenges of the future with the help of cutting-edge tools like artificial intelligence and simulation. Travancore Analytics provides an advanced digital twin solution that integrates superior simulation, artificial intelligence, data analytics, and high-performance computing to foster innovation, save time, and minimize waste.