May 27th, 2025
Category: IoT
No Comments
Posted by: Team TA
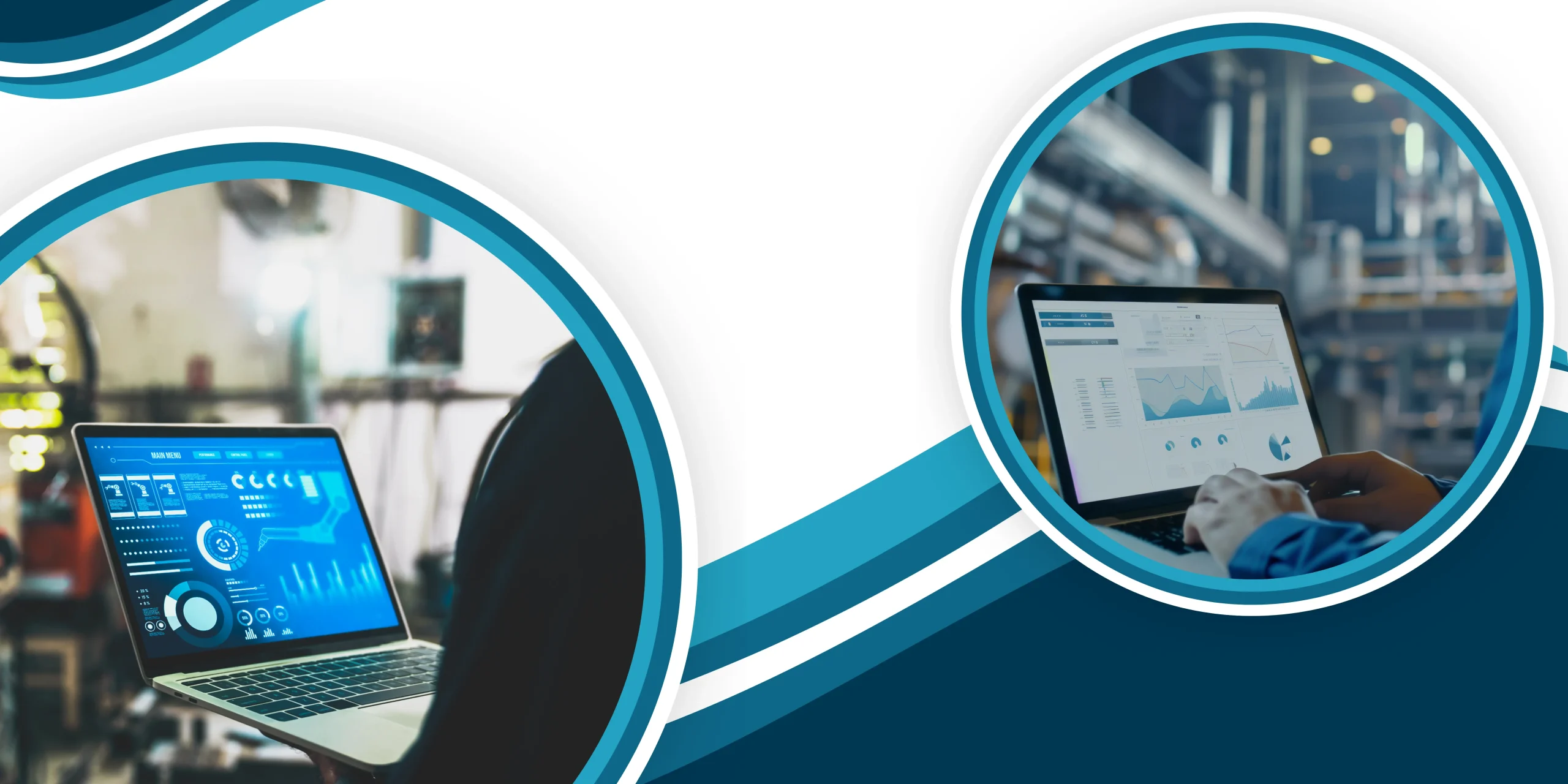
Unplanned downtime can significantly cripple productivity and reduce profits in today’s fast-paced manufacturing environment. From sudden machine failures to unattended faults, these disruptions can cost businesses heavily. According to a Siemens report from 2024, unplanned downtime now costs the world’s 500 largest companies an astonishing 11% of their revenues, amounting to a staggering total of $1.4 trillion. This alarming statistic emphasizes how urgently manufacturers must adopt more intelligent solutions that ensure uninterrupted operations.
With real-time analytics and predictive insights, the Internet of Things (IoT) revolutionizes manufacturing by enabling zero downtime. IoT enables proactive maintenance, rapid fault detection, and continuous monitoring by integrating sensors and networked devices into machinery. This article explores how IoT is transforming manufacturing by reducing disruptions and optimizing efficiency like never before.
Real-Time Analytics and IoT for Smart Manufacturing
The global market for IoT in manufacturing was estimated by Fortune Business Insights to be worth $97.03 billion in 2023 and is projected to reach $673.95 billion by 2032. By using smart sensors to connect workers, systems, and machines, IoT is redefining the manufacturing industry. Manufacturers are better able to monitor machine performance, identify issues early, and act quickly thanks to the real-time connectivity.
Real-time data allows manufacturers to identify problems before they turn critical. IoT-powered predictive maintenance lowers unscheduled breakdowns, increases efficiency, and improves safety. As a result, IoT assists in pre-scheduling maintenance, minimizing expensive downtime, and maintaining reliable and effective production.
Manufacturers can see what’s going on the factory floor at any time with the help of real-time analytics. It reveals real-time information on the performance, health, and problem areas of the machine. This aids teams in making prompt, intelligent decisions to prevent malfunctions, enhance equipment utilization, and maintain uninterrupted production. Decision-making would be challenging without real-time insights; hence, they are crucial for dependable and effective manufacturing processes.
How IoT-Powered Real-Time Analytics Reduce Downtime?
1. Real-Time Data Monitoring
By continuously monitoring machine conditions like temperature, vibration, and pressure, IoT helps manufacturers minimize downtime. These sensors immediately notify the maintenance crew of any suspicious changes. This enables prompt action before an issue develops into an expensive breakdown. For instance, a spike in vibration may indicate a worn-out component that can be replaced early, preventing unexpected halts in production.
Manufacturers can make quicker decisions and better plans thanks to these real-time insights, which provide a clear, live view of all the equipment throughout the plant. Teams can plan fixes during scheduled downtimes rather than responding to failures. In addition to lowering unscheduled stops, this proactive strategy increases productivity and prolongs machine life.
2. Advanced Data Analytics
Advanced data analytics and IoT enable manufacturers to identify issues before they occur. Managers can anticipate equipment failures and take early action by analyzing patterns in sensor data. This preventative strategy lowers unplanned breakdowns and maintains production efficiency. According to McKinsey, advanced analytics can increase equipment life by about 40% and reduce downtime by 30 to 50%.
Teams can better plan maintenance, enhance equipment performance, and cut down on expensive delays with real-time reports and predictive insights of IoT-driven analytics. With fewer disruptions and more effective operations, these intelligent systems help manufacturers optimize processes and increase productivity by transforming raw data into actionable steps.
3. Predictive Maintenance
IoT-powered predictive maintenance helps manufacturers shift from reactive fixes to proactive care. To predict when a part might fail, smart sensors gather and analyze real-time data on machine conditions, like temperature, vibration, and pressure. This minimizes downtime and prevents unplanned breakdowns by enabling maintenance scheduling just-in-time.
Predictive algorithms use real-time and historical data to identify problems early and notify teams before failures occur. Scheduled stops, rather than emergency halts, can then be used for maintenance. This guarantees seamless, continuous production, lowers maintenance costs, and increases asset reliability.
4. Automated Alerts and Diagnostics
By immediately alerting technicians when a machine exhibits symptoms of trouble, IoT devices with automated alerts help minimize downtime. These notifications, which are sent to computers or mobile devices, guarantee prompt action before minor problems get any worse. For instance, a sensor that detects vibration or high pressure instantly sounds an alert, allowing for immediate action and preventing unplanned malfunctions.
IoT systems log error codes and detailed data to provide remote diagnostics in addition to alerts. This helps technicians quickly identify the root cause and carry the right tools, reducing repair time and keeping production on track.
5. Quality Assurance Insights
By employing real-time analytics to ensure steady product quality, IoT helps minimize manufacturing downtime. Smart sensors track key variables like temperature, speed, or humidity and alert teams immediately if something goes off track. This avoids production halts for rework or quality investigations by enabling prompt adjustments before minor problems turn into major flaws.
IoT reduces the need for manual quality checks by maintaining processes within ideal ranges. Over time, the data also reveals patterns that help fix recurring quality issues, leading to smoother operations and fewer unplanned stops.
6. Process Optimization and Bottleneck Reduction
By exposing hidden inefficiencies in production processes, IoT assists manufacturers in minimizing downtime. Teams can identify trends like recurring micro-stoppages or speed discrepancies by examining sensor data from various machines. Resolving these minor problems, like faulty jam signals or struggling stations, can result in significant time savings and more efficient operations.
Managers can also optimize workflows and schedules with the aid of advanced IoT analytics. For example, total downtime can be decreased by synchronizing machine speeds or consolidating maintenance tasks into a single stop.
5 Benefits of Real-Time Analytics on Manufacturing
1. Improving Production Efficiency
Manufacturers can make quick decisions to optimize operations by using real-time analytics, which gives them instant visibility into production metrics. Teams can improve throughput, increase machine utilization, and cut waste by spotting bottlenecks, inefficiencies, and patterns of energy consumption as soon as they appear. In addition to increasing productivity, this lowers operating expenses and advances sustainability objectives.
2. Strengthening Quality Assurance While Minimizing Product Waste
Real-time analytics in manufacturing makes it possible to identify flaws early in the production process. Real-time insights, fueled by sensors and computer vision, detect problems as they occur, in contrast to conventional approaches that detect problems after they occur. As a result, waste is decreased, rework is reduced, and product quality is maintained throughout the manufacturing process.
3. Maximizing Resource Utilization
Real-time analytics help manufacturers allocate resources more efficiently by giving them instant insights into labor, equipment performance, energy consumption, and material use. This leads to better decisions that reduce waste and boost productivity. It facilitates inventory control and energy optimization, which lowers costs and improves production efficiency.
4. Extending Equipment Life
Data analytics is a useful tool for tracking and evaluating the condition and usage of equipment as well as identifying usage patterns. Manufacturers can extend the lifespan of vital machinery by knowing how it is used and maintained. By redistributing workloads, following maintenance schedules, and taking preventive measures, manufacturers can extend the useful life of their machinery.
5. Lowering Operational Expenses
By facilitating predictive maintenance, decreasing downtime, and increasing equipment lifespan, data analytics offers a strong return on investment (ROI) and helps manufacturers save a lot of money. Additionally, it enhances asset utilization and energy efficiency. Beyond cost savings, it increases productivity and throughput without needing infrastructure expansion. This assists manufacturers in strengthening their profitability and increasing revenue through more intelligent, data-driven operational strategies.
Final Thoughts
In conclusion, IoT-powered real-time analytics is transforming the manufacturing industry by enabling continuous operations without downtime. Smart sensors actively monitor equipment and processes, allowing manufacturers to identify and address problems early on. This proactive approach improves equipment uptime, reduces costs, and enhances overall efficiency. Additionally, real-time data facilitates quicker decision-making, ongoing process improvements, and better resource management, making these advantages crucial in today’s competitive market. Discover how Travancore Analytics can empower you to tap into real-time analytics, allowing you to cut costs and elevate your bottom line to new heights!